What is insulation tape?
Insulation tapes play a crucial role in HVAC systems, electrical applications, and repair work, ensuring efficiency, safety, and durability. Whether it’s sealing air ducts, protecting electrical wiring, or reinforcing joints, the right insulation tape enhances performance and extends the lifespan of systems.
For HVAC professionals, electricians, and maintenance teams, choosing the correct insulation tape can prevent air leaks, improve thermal efficiency, and ensure electrical safety. But with so many options available, how do you know which one fits your needs?
Definition and purpose
Insulation tape is a specialized adhesive tape designed to provide thermal, electrical, and mechanical protection across various applications. It plays a critical role in HVAC systems, electrical wiring, and industrial repairs, ensuring components are protected against heat, moisture, and external damage.
Unlike standard adhesive tapes, insulation tapes are made from heat-resistant, durable materials that maintain strong adhesion even in harsh conditions.
Key materials used in insulation tapes
Depending on the application, insulation tapes are made from different materials, each offering unique benefits:
PVC Tape – Common in electrical insulation, PVC tapes provide high dielectric strength, flexibility, and resistance to moisture and abrasion.
Aluminum Foil Tape – Used in HVAC sealing, these tapes are highly heat-resistant, reflective, and provide excellent air and moisture sealing.
Butyl Rubber Tape – Ideal for HVAC duct sealing and waterproofing, known for its strong adhesion and flexibility.
Self-Fusing Silicone Tape – A go-to for high-temperature insulation and emergency repairs, offering heat and chemical resistance without needing adhesives.
How Insulation Tapes Differ from Standard Adhesive Tapes
While traditional adhesive tapes focus on basic bonding, insulation tapes are designed for specific technical applications:
Feature | Insulation tape | Standard Adhesive Tape |
Temperature resistance | High (can withstand heat and cold) | Limited |
Adhesive Strength | Engineered for long-term durability | General-purpose |
Moisture resistance | Waterproof & airtight options available | Varies |
Application | HVAC sealing, electrical insulation, repair | Basic bonding & packaging |
By choosing the right insulation tape, industries can ensure better system performance, energy efficiency, and long-term protection.
HVAC insulation tapes: sealing & thermal efficiency
Why HVAC insulation tapes matter
In HVAC (Heating, Ventilation, and Air Conditioning) systems, proper sealing and insulation are essential for energy efficiency, performance, and durability. Leaks in ducts and pipes can cause energy loss, reduced system efficiency, and increased operational costs. HVAC insulation tapes help seal joints, prevent air leakage, and maintain optimal thermal performance.
By using high-quality insulation tapes, HVAC professionals can:
- Improve energy efficiency by reducing air loss.
- Prevent condensation buildup, which can lead to mold and corrosion.
- Ensure long-term durability of ductwork and ventilation systems.
Key applications of HVAC insulation tapes
Sealing air ducts & ventilation systems
One of the most common uses of insulation tapes in HVAC systems is sealing duct joints to prevent air leaks. Proper sealing:
- Reduces energy waste by maintaining airflow efficiency.
- Helps meet building regulations and energy standards.
- Improves air quality by preventing dust or contaminants from entering the system.
Insulating pipes & refrigeration lines
HVAC systems often use insulated pipes to maintain temperature stability. Insulation tapes help:
- Prevent heat loss or gain, ensuring efficient heating or cooling.
- Minimize condensation, reducing the risk of water damage.
- Provide UV resistance for outdoor applications.
Securing Insulation Materials
Foam or fiberglass insulation wraps are used around pipes and ducts, but they require reinforcement. HVAC insulation tapes secure these materials in place, ensuring long-term performance.
Types of HVAC insulation tapes
Aluminum foil tape – High heat resistance
- Ideal for sealing HVAC ducts and ventilation systems.
- Provides excellent heat reflection and moisture resistance.
- Used in high-temperature environments.
Butyl rubber tape – Superior airtight sealing
- Highly flexible and perfect for air and moisture sealing.
- Provides long-term adhesion, even in extreme conditions.
- Commonly used for outdoor HVAC applications.
PVC insulation tape – moisture & corrosion protection
- Protects pipes and fittings from condensation buildup.
- Offers strong resistance to moisture and chemicals.
- Used for general HVAC insulation and securing wraps.
Best practices for applying HVAC insulation tapes
To ensure maximum sealing performance, follow these best practices:
- Clean the surface – Remove dust, grease, and moisture before application.
- Apply with tension – Stretch the tape slightly to create a tight, secure bond.
- Use multiple layers – For added durability, apply overlapping layers when necessary.
- Choose the right tape – Select a tape based on temperature resistance, moisture exposure, and adhesion strength.
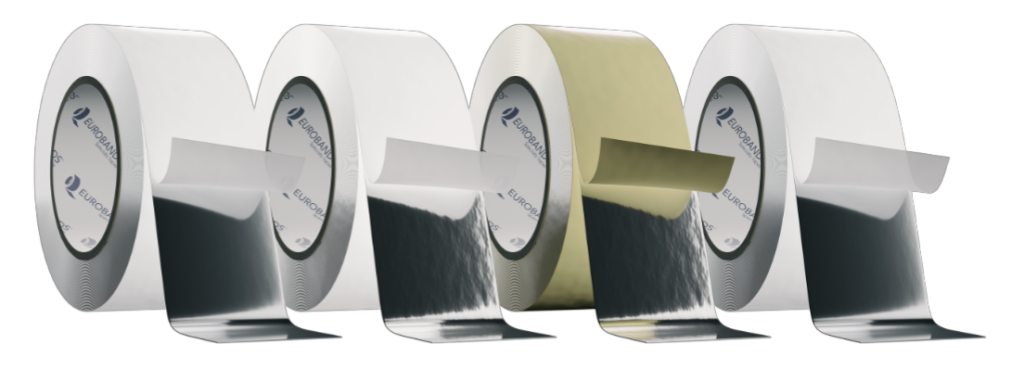
Electrical Insulation Tapes: Safety & Protection
Why electrical insulation tapes matter
Electrical systems require high-performance insulation to prevent short circuits, electrical failures, and safety hazards. Electrical insulation tapes are designed to protect wiring, provide insulation, and ensure long-lasting durability in various applications, from low-voltage wiring to high-voltage industrial systems.
By using the right electrical insulation tape, professionals can:
- Prevent electrical hazards such as short circuits and wire damage.
- Ensure proper insulation for long-term system reliability.
- Protect against moisture, heat, and chemical exposure.
Key applications of electrical insulation tapes
Wire Bundling & Cable Organization
Electrical tapes are used to group and secure wires together, preventing tangling and making maintenance easier.
- Helps organize electrical systems for easy identification.
- Reduces wear and tear by keeping cables properly aligned.
- Common in panel boards, control systems, and home wiring.
Insulating Electrical Connections
Proper insulation prevents electrical failures caused by exposed or damaged wires. Electrical tapes:
- Cover spliced wires and exposed conductors to prevent short circuits.
- Provide dielectric protection, reducing the risk of electrical shocks.
- Enhance safety in industrial and household electrical systems.
High-Voltage Insulation & Repair
- For high-voltage applications, specialized insulation tapes provide added protection against heat and electrical stress.
- Used in transformers, motor windings, and high-voltage connectors.
- Heat-resistant tapes ensure reliable insulation in extreme conditions.
Types of electrical insulation tapes
PVC electrical insulation tape – versatile & reliable
- The most commonly used insulation tape for general electrical wiring.
- Offers good dielectric strength, flexibility, and moisture resistance.
- Ideal for low to medium voltage applications.
Rubber-based insulation tape – High-voltage protection
- Self-fusing rubber tapes are used for high-voltage insulation.
- Provides superior resistance to heat, moisture, and corrosion.
- Common in industrial power distribution and transformer insulation.
Heat-resistant silicone tape – extreme condition protection
- Withstands high temperatures and harsh environments.
- Used in aerospace, automotive, and industrial applications.
- Provides permanent bonding without adhesives, fusing to itself when wrapped.
Best practices for applying electrical insulation tapes
To ensure maximum safety and performance, follow these best practices:
- Clean the surface – Wipe down cables and connectors before applying tape.
- Stretch & wrap properly – Stretch the tape slightly as you wrap to create a tight, secure bond.
- Layer for extra insulation – For high-voltage applications, apply multiple layers for added protection.
- Use the right tape for the voltage level – Choose a high-voltage-rated tape when needed
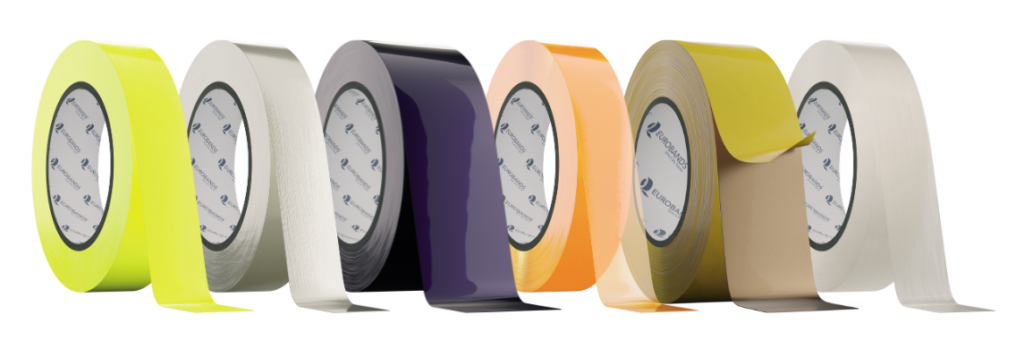
Joining & repair tapes: durable bonding solutions
Why joining & repair tapes matter
Insulation tapes aren’t just for sealing and electrical protection—they also play a critical role in joining, repairing, and reinforcing components in industrial, HVAC, and electrical applications. High-performance repair tapes provide a strong, durable bond that withstands heat, moisture, and mechanical stress, making them essential for quick fixes and long-term solutions.
By using joining and repair tapes, professionals can:
- Reinforce and repair damaged insulation on pipes, ducts, and cables.
- Create strong, flexible joints that resist wear and tear.
- Ensure airtight and waterproof seals in critical areas.
Key applications of joining & repair tapes
Pipe & Duct Repair in HVAC Systems
Damaged HVAC ducts or insulation layers can lead to air leaks, reduced efficiency, and increased energy costs. Repair tapes:
- Seal cracks, holes, or worn-out insulation layers in ducts and pipes.
- Prevent air loss and condensation buildup, maintaining HVAC efficiency.
- Provide a strong, weather-resistant bond for outdoor applications.
Emergency Electrical Repairs & Wire Reinforcement
For damaged or exposed electrical cables, repair tapes provide a quick, insulated fix:
- Self-fusing silicone tapes wrap around exposed wires, providing instant insulation.
- Rubber-based repair tapes withstand high-voltage stress for industrial applications.
- Prevent short circuits and enhance electrical safety.
Industrial & Automotive Sealing Applications
Joining and repair tapes are also used in automotive, aerospace, and manufacturing for:
- Sealing fluid-carrying pipes to prevent leaks.
- Reinforcing mechanical joints to withstand vibration and stress.
- Weatherproofing components exposed to extreme conditions.
Key applications of joining & repair tapes
Self-fusing silicone tape – Quick & permanent repairs
- Bonds instantly without adhesives by fusing to itself.
- Provides heat, moisture, and chemical resistance.
- Ideal for emergency repairs on pipes, hoses, and electrical wiring.
Reinforced insulation tape – Heavy-duty durability
- Contains woven reinforcement for added strength.
- Used in high-stress industrial applications.
- Resistant to abrasion, heat, and solvents.
High-tack butyl tape – Waterproof & airtight sealing
- Creates a strong, flexible seal on ducts, joints, and mechanical components.
- Maintains adhesion in hot, humid, or wet conditions.
- Perfect for HVAC and outdoor applications.
Best practices for using repair & joining tapes
For maximum adhesion and durability, follow these best practices:
- Clean the Surface – Remove dirt, grease, and debris for a stronger bond.
- Stretch and Wrap Firmly – Apply tension while wrapping for a secure seal.
- Layer for Added Strength – For high-pressure or high-heat applications, apply multiple overlapping layers.
- Select the Right Tape for the Job – Choose heat-resistant, waterproof, or self-fusing options depending on the environment.
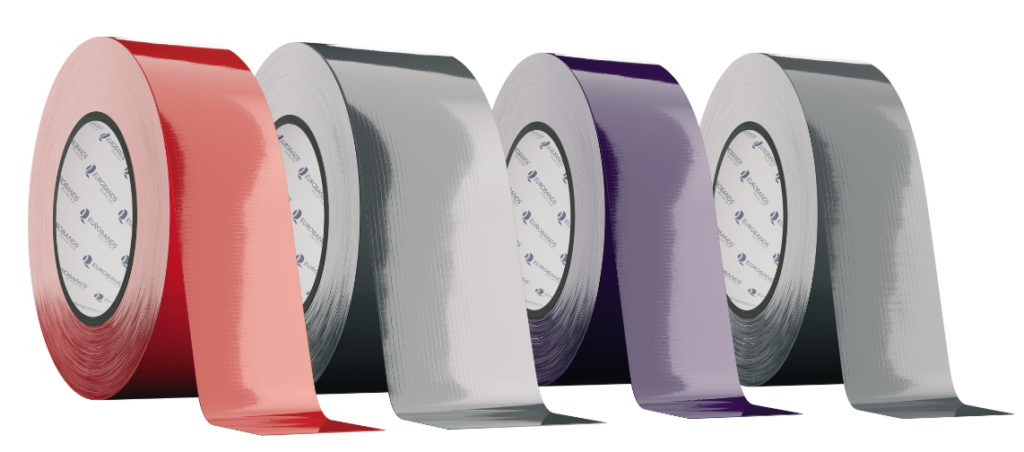
How to choose the right insulation tape
Selecting the right insulation tape depends on several key factors, including application type, temperature resistance, adhesion strength, and environmental conditions. Whether you need insulation for HVAC sealing, electrical protection, or industrial repairs, choosing the correct tape ensures maximum efficiency and durability.
Factors to consider when choosing insulation tape
Application type – What is the tape being used for?
- HVAC sealing: Requires high-temperature resistance, strong adhesion, and airtight sealing.
- Electrical insulation: Needs high dielectric strength, flexibility, and fire resistance.
- Joining & repairs: Demands strong adhesion, moisture resistance, and durability.
Adhesive strength – How well does it bond to surfaces?
- Rubber-based adhesives: High flexibility and strong adhesion for electrical and general insulation.
- Butyl adhesives: Best for HVAC and duct sealing, providing long-term airtight protection.
- Acrylic solvent adhesives: Ideal for high-temperature applications, ensuring heat and chemical resistance.
Temperature & Environmental Resistance
- For HVAC systems, tapes must withstand temperature fluctuations, moisture, and UV exposure.
- For electrical insulation, tapes should be fire-resistant and capable of handling high voltages.
- For outdoor applications, UV-resistant and waterproof properties are essential.
Surface Compatibility – Will the tape adhere properly?
- Smooth surfaces (metal ducts, electrical wires) require strong adhesion with flexibility.
- Textured or rough surfaces need high-tack adhesives to ensure lasting bonds.
FAQ - Insulation tapes explained
Insulation tape is designed to protect, insulate, and secure electrical connections, pipes, and surfaces. It is commonly used for:
- Electrical insulation – Preventing short circuits and ensuring safe wiring.
- HVAC sealing – Sealing duct joints to prevent air leaks and improve energy efficiency.
- Thermal protection – Providing heat resistance for wiring, components, and pipes.
- Moisture and weatherproofing – Protecting electrical and mechanical connections from humidity and environmental exposure.
Different types of insulation tapes cater to various industries, from construction and HVAC to automotive and electronics.
Yes, insulation tape is a cost-effective and efficient solution for enhancing safety, durability, and energy efficiency in many applications. Key benefits include:
✔ Electrical safety – Reduces the risk of shocks and short circuits.
✔ Energy efficiency – Helps maintain proper insulation in HVAC systems.
✔ Protection from wear and tear – Shields wires, pipes, and components from environmental damage.
✔ Easy application – Simple to use and apply, reducing labor costs.
Choosing the right high-quality insulation tape ensures long-lasting protection and performance.
Yes, weather-resistant insulation tape is specifically designed to withstand harsh environmental conditions, including:
🌧 Rain & Moisture – Prevents water ingress and corrosion.
☀ Heat & UV Exposure – Resists high temperatures and sun damage.
❄ Cold & Freezing Conditions – Maintains flexibility and adhesion even in extreme cold.
💨 Wind & Dust Protection – Seals gaps in HVAC systems, preventing air leaks.
For outdoor or extreme conditions, specialized weatherproof insulation tapes provide reliable long-term performance.
Insulation tape is a pressure-sensitive adhesive tape designed to insulate, protect, and secure electrical wires, HVAC ducts, and other components. It comes in various materials, including:
- PVC Insulation Tape – Common for electrical wiring due to flexibility and durability.
- Foil Insulation Tape – Used for HVAC applications and heat-reflective sealing.
- Rubber & Silicone Tapes – Provide strong sealing and resistance to extreme temperatures.
Its primary purpose is to prevent electrical hazards, improve thermal insulation, and enhance durability in industrial and residential settings.
High-quality insulation tape is safe when used correctly. It is flame-retardant, electrically resistant, and durable, offering:
✔ Shock prevention – Protects users from exposed electrical wiring.
✔ Heat resistance – Withstands temperature variations in electrical and HVAC applications.
✔ Chemical & moisture protection – Prevents damage from environmental exposure.
To ensure maximum safety, always use tape rated for your specific application, and avoid using general-purpose tape for electrical work.